背景
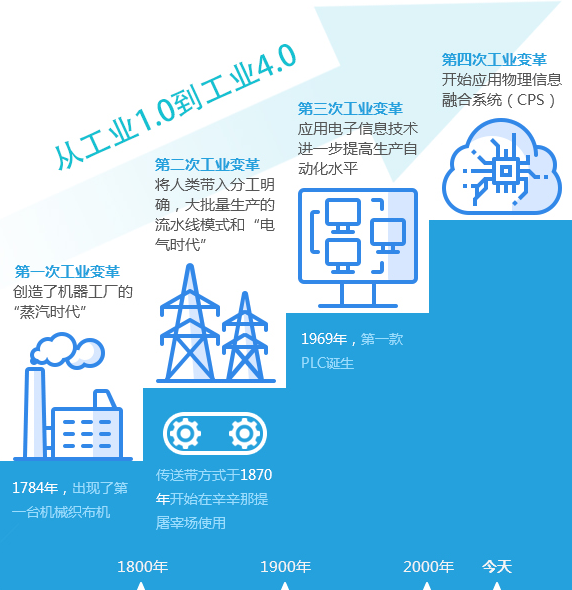
过去工厂
- 物料传输缺乏自动化
- 手写记录卡片在晶圆盒上
- 只有基本的设备标准
- 原始的设备控制
- 原始的制造解决方案
现代工厂
- 物料传输开始自动化
- 将基于统计数字的流程控制自动化
- 改进设备控制
- 改善库存控制和跟查
- 提高设备自动化的标准
- 高度整合的工厂运行解决方案
- 规划和供应链整合
- 改进决策系统
智能工厂
- 普及使用自动化的物料传输
- 普及使用标准化的设备
- 先进的生产执行方案
- 实时的异常情况控制系统
- 先进的流程控制和调整
- 预测式和灵活的维护
- 先进快速的决策
- 大数据存储
- 物联网与工业设备集成
工厂待解决的问题
管理层面
人工收集机台加工实际数据,无法实时统计机台产能和稼动率
手工收集发布机台故障信息,无法在第一时间反馈机台信息
安排人力整场巡视,手动收集机台加工作业信息和状态信息,准确性和实时性都无法保障
受制于技术和开发,新的应用无法及时完成,导致验证周期过长
生产层面
生产机台设备运行,只能通过现场机器屏幕看到,无法进行远程查看设备运行的详细状态及运行参数
每台机器都有其运行特点,人工无法精确统计每台机器的运行合理参数精确范围
机台历史数据没有系统备份,不方便维修和故障诊断,多数情况是根据现场维护人员经验决定维护质量
无预测性维护,只能等问题发生,然后处理维护,效率提升困难。
生产中,无法通过机台参数判断主要耗材,例如刀具状态、断刀,崩刃等
主要耗材例如刀具寿命,通过经验,无法精准判断寿命
没有及时的基础数据分析,延迟管理决策
基本功能
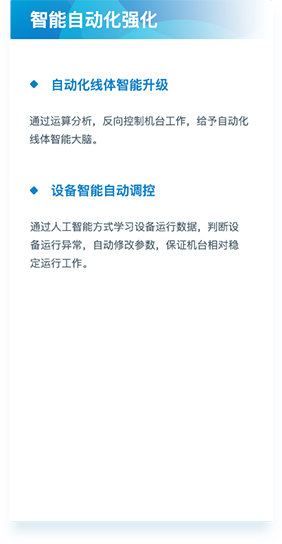
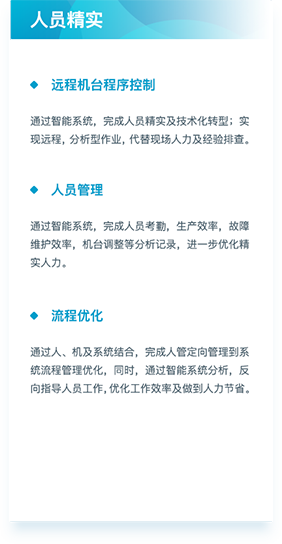
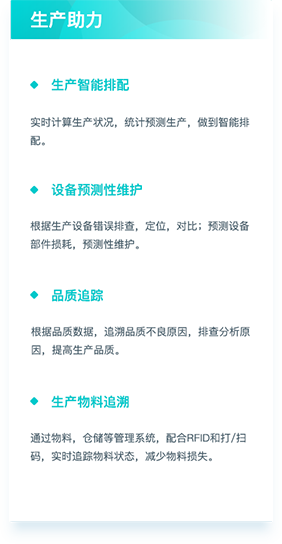
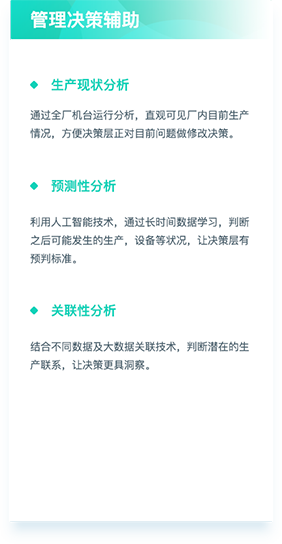
实际价值
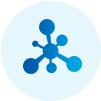
10%
主要耗材的节省 例如:刀具
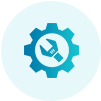
20%
主要设备使用寿命的增加 例如:CNC机台
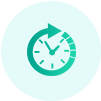
30%
EVT(上线验证时间)的节省
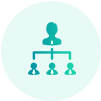
40%
人力的节省
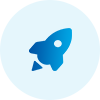
50%
决策效率的提高
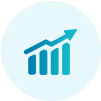
3%
良品率的提高